How Smart Building Technology Can Help Solve Predictive Maintenance Shortcomings
Predictive maintenance for smart building assets isn’t new. However, time-consuming manual processes, false positives/negatives, and poorly documented predictive maintenance remediation tasks have left much to be desired. Thankfully, artificial intelligence (AI) is coming to the rescue, and smart building predictive maintenance will undoubtedly never be the same.
Let’s look at faults within existing predictive maintenance processes and systems and how AI can bolster those deficiencies.
Predictive Maintenance Process and Tool Shortcomings
The moment an IT or OT asset is deployed within a building, the mean time to failure (MTTF) clock starts ticking. For those who aren’t aware, MTTF is a metric that measures the average amount of time a particular digital or mechanical component will function before something fails.
While the MTTF metric is useful for “big picture” predictions, building professionals rely on smart building technologies more than ever. As such, building management systems (BMS) and other monitoring tools collect smart building health information. Maintenance teams then create manually configured alert triggers to notify IT and facilities staff when a monitored metric threshold is surpassed. This often indicates that an IT/OT asset has an issue that needs to be addressed before a catastrophic failure.
The other aspect that plagues existing predictive maintenance accuracy and, thus, its usefulness is that not enough system and component data is being collected and analyzed. While plenty of information can be collected from the IT/OT system itself, many external factors that can contribute to premature system failures are not being monitored. This lack of a “wider lens” of component health visibility leads to faults that could have been spotted and preemptively addressed—but failures still occurred.
Enhancing Fault Visibility and Making Sense of Data
The combination of IoT sensors, artificial intelligence and machine learning (ML) can take what’s possible today with predictive maintenance and put it on overdrive. For instance, smart building systems can have IoT sensors within and around equipment to collect real-time data about its operating conditions. These sensors can monitor temperature, humidity, vibration and energy consumption, for example.
However, the problem with having more data to work with is that someone or something must have the intelligence to analyze it and make sense of it all. This is where AI and ML come into play. Using AI to analyze the collected data using machine learning algorithms, intelligent preemptive maintenance systems can autonomously identify patterns indicative of potential failures or degradation in performance.
For example, if IoT sensors collect abnormal vibration pattern data within HVAC units, AI can identify this vibration change based on historical information. Then, not only can the predictive maintenance system alert on the issue, but also it can also better pinpoint the root cause of the variance or fault and provide details on how the issue can best be resolved.
Potential Cost Savings
Identifying faults early on—especially within mechanical systems—can lead to low-cost and small repairs without significant downtime or chain reaction faults. Thus, not only does preemptive maintenance better guarantee smart building IT/OT uptime, but it also results in cost savings due to the rapid identification and remediation of minor faults before they result in major faults.
Although far from fool-proof, AI and IoT can fill in the gaps where traditional predictive maintenance solutions fall short to make your buildings smarter and more efficient.
About the Author
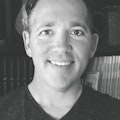
Andrew Froehlich
Contributor
As a highly regarded network architect and trusted IT consultant with worldwide contacts, Andrew Froehlich counts over two decades of experience and possesses multiple industry certifications in the field of enterprise networking. Andrew is the founder and president of Colorado-based West Gate Networks, which specializes in enterprise network architectures and data center build-outs. He’s also the founder of an enterprise IT research and analysis firm, InfraMomentum. As the author of two Cisco certification study guides published by Sybex, he is a regular contributor to multiple enterprise IT-related websites and trade journals with insights into rapidly changing developments in the IT industry.